FUEL DISTRIBUTION AND STORAGE SYSTEMS
As I pointed out in a prior article, fuel is in a constant state of flux. From the time it leaves the refinery, through every point of transfer it is exposed to contamination. Once refined, fuel moves through the transportation system until it reaches its final destination. Delivery might include pipeline, ship, barge, tanker or rail car before arriving at its final point of use. Fuels may be allowed to settle prior to being shipped to the next destination but this is not a guarantee. Settling is important as it permits contaminants to fall out and be pumped off. Without proper settling, contamination is transferred.
Many of the components of the fuel distribution system are made up of low or mild carbon steel making tanks, pipes and pumps very susceptible to corrosion, especially microbial influenced corrosion (MIC). Rust and metal particulates are frequently carried downstream to end users. Water continues to be a problem. Throughout the distribution system water can be transferred along with fuel. Pipeline cleaning, called pigging, contributes to higher contamination levels. If filtration is a part of the distribution chain, it may not be adequate. By the time fuel reaches the end user it likely does not meet current engine manufacturer specifications. BP completed a study on retail diesel fuel in 2007 that confirmed fuel sold at retail did not meet recommended OEM specifications. Since then, little has been done to improve product quality to the end user. This is why there are growing concerns for cleaner, dryer fuels. Driven by consumer demand, wholesalers and retailers are taking up the banner of fuel quality management.
Understanding basic fuel storage system design and the challenges to providing clean, dry fuel are the first steps to fuel quality management. The anatomy of a fuel system will vary from site to site. There are above ground storage tanks (AST) and underground storage tanks (UST) as well as specialty tanks of all kinds. They can be vertical or horizonal. Some ASTs are tilted for easy water drainage. Even with a variety of types and applications, there are enough commonalities to draw assumptions and disseminate accurate information. As stated, contamination is moved along the transportation system until it finds its resting place with the end user. These contaminants continue to collect and multiply when left unchecked. Greater accumulation plus the time left between maintenance cycles equals higher costs to both the fuel system owner and the end user. Cost reduction includes a basic understanding of fuel system design. We will review the typical downstream application including tanks, access points, piping and pumping components. A little working knowledge helps to identify potential contamination problems and create a fuel quality management program that works.
Tanks and Access Points
As previously mentioned, the two major tank types are UST and AST systems. Both have advantages and disadvantages. Application often dictates which type is used. Land cost, space availability and transportability and environmental factors all play a role in determining which type of tank system is chosen. Whether an AST or UST, there are typical layouts. The diagram above shows a typical tank setup and some of the potential contamination related issues.
6 Basic Facts related to tank contamination
- Water is always present in one form or another. Both AST and UST systems condensate. AST systems are potentially more exposed to environmental changes than UST tanks. Extreme vacillations in temperature are not uncommon. In regions where temperatures are high, microbial growth is accelerated. Knowing the type of tank and the conditions it is exposed to can help anticipate and identify potential problems.
- Tank strike plates and limited access create challenges for obtaining good fuel samples and identifying the presence of water. Strike plates are a minimum of ¼” thick and are found under tank access points. If you are sampling from an access point over a strike plate then you will not recognize water or contamination until it breaches the strike plate level. It is possible to have a strike plate under all access points. Limited access reduces your ability to view and sample the inside of the tank without special, usually expensive, equipment.
- USTs generally settle over time. Depending on the angle, water and other contaminants settle to the lowest end of the tank often out of reach or sight. Knowing the tilt of a tank is imperative to fuel quality management.
- Probe failure and false readings are not uncommon. Contamination will damage probes and probe floats. Depending solely on automatic tank gauge systems is a mistake. There is no substitute for regular fuel sampling and physical inspections.
- Drop tubes, when fuel is delivered, tend to agitate settled contaminants and push contamination away from product fills. That being the case, sampling only from the fill will likely produce inaccurate samples. It is always best to take multiple samples from as many access points as possible and from bottom, mid and top layers of the fuel.
- Beware of baffles. There can be tank baffles that impede access and cleaning. They hide contamination and make it difficult, if not impossible to properly clean and maintain. The picture of a baffled tank with limited access is one example of many. This specific tank had two access points at each side of the tank baffles of the tank. Many baffled tanks do not adequate access.
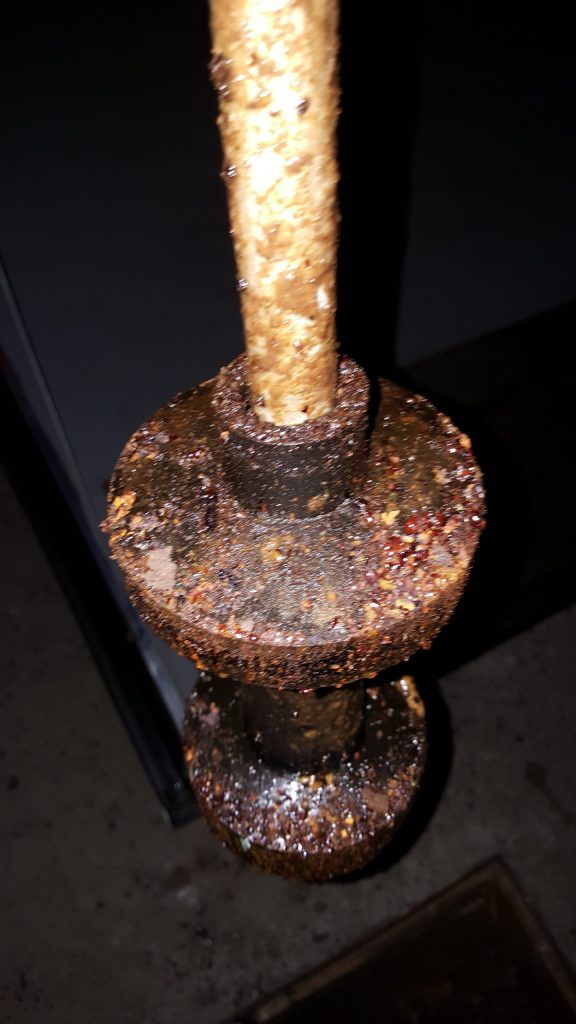
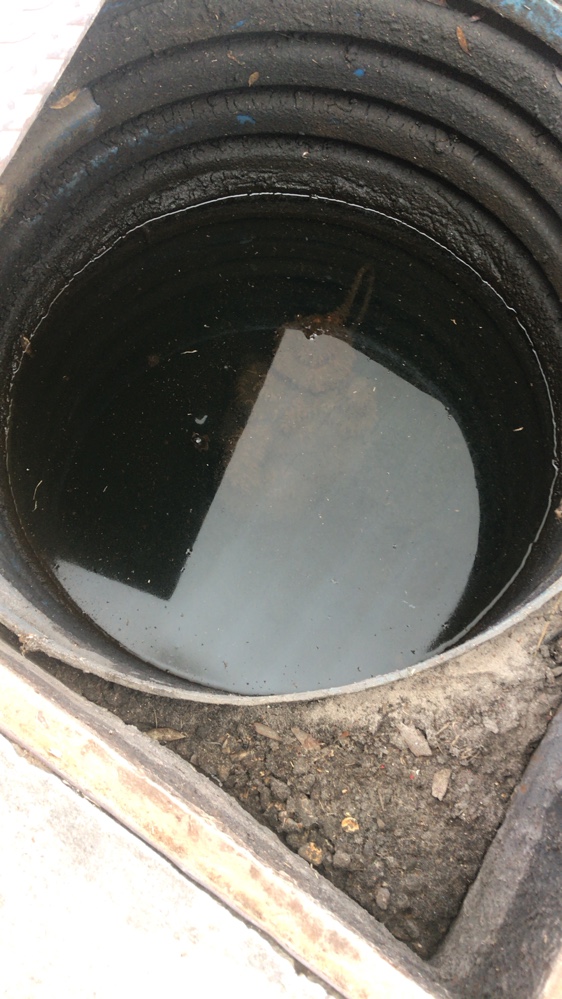
Piping
There are different types of piping ranging from ridged to flexible. They are made from steel, fiberglass, and polyethylene to name a few. No matter the kind of piping, construction and installation can have a lot to do with how a system harbors contamination – especially microbial. Any settling, dips or low points in the piping system offers a place for contaminants to collect and grow. Biofilms form in these low spots and become a host for microbial colonies. The Coordinating Research Council report on diesel fuel storage and handling finds it is nearly impossible to properly maintain a fuel system without the use of biocides. The only way to reach pockets of microbial contamination is to use a biocide like Biobor®JF that is soluble in both water and fuel. It is carried along with the fuel throughout the system, killing microbes along the way. Polish your fuel – great; clean your tank – great; use a biocide to sterilize the system and fuel – better!
Pumping Components
Fuel dispensers, submerged turbine pumps (STP), nozzles and hanging hardware are all affected by contamination. Dirty fuel will relate to higher maintenance costs. If you do not have a fuel quality management program in place then you are already seeing some of the major warning signs.
12 Fuel System Warning Signs
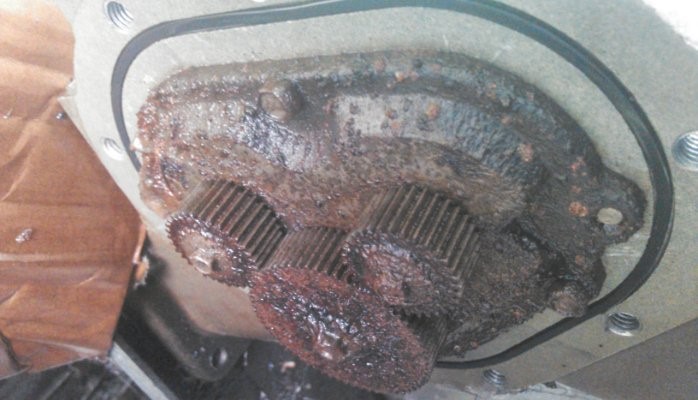
- Premature dispenser filter replacements
- Corroded dispenser filters
- Dispenser meter replacements due to MIC
- Corroded STP components
- Dispenser overruns
- Frequent or repeated proportional valve replacement
- Slow flow issues
- Premature and repeated hanging hardware failures
- Leak detector failures
- Shear valve failure
- Line and tank failure
- Probe failure
You can bet that your contamination issues are costing you money – studies show upwards of 35% higher maintenance costs due to contaminated fuel. Removing water and using a quality biocide like Biobor®JF will save you money. The cost to remove free water and periodically dose your fuel with biocide is small compared to the savings you will realize in lower maintenance costs. Each time you call a technician out to perform a fuel quality related task you are likely spending more than it costs to dose your system with biocide.
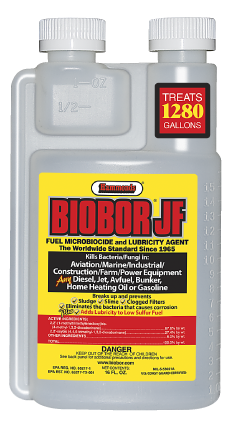
Biobor JF is the original, industry standard biocide since 1965. Independently tested, EPA registered and OEM approved for use in all hydrocarbons. It does not affect fuel performance and is more stable, less corrosive and safer to handle than other products on the market. It works in both water and fuel unlike many of our competitors. You want to use a biocide that moves through the fuel system with the fuel and continues to kill microbial contamination along the way.
Follow BioborShare the Post