Hurricane Elsa was the earliest Atlantic hurricane to form since Emily in 2005. Although not a strong storm with the estimated damages of almost $230 million. The rainfall totals were high, averaging over 11″ in some areas. To give you some idea of the magnitude of the rain fall, a 7″ rain over a small building lot of 120’x120′ would equate to 62,832 gallons of water. For an underground storage system, this amount of water often poses a serious problem. Even the best built facilities can have problems mitigating that much water in a short period of time. That is why water management needs to be an integral part of your fuel management program.
Four Fundamentals to Water Management
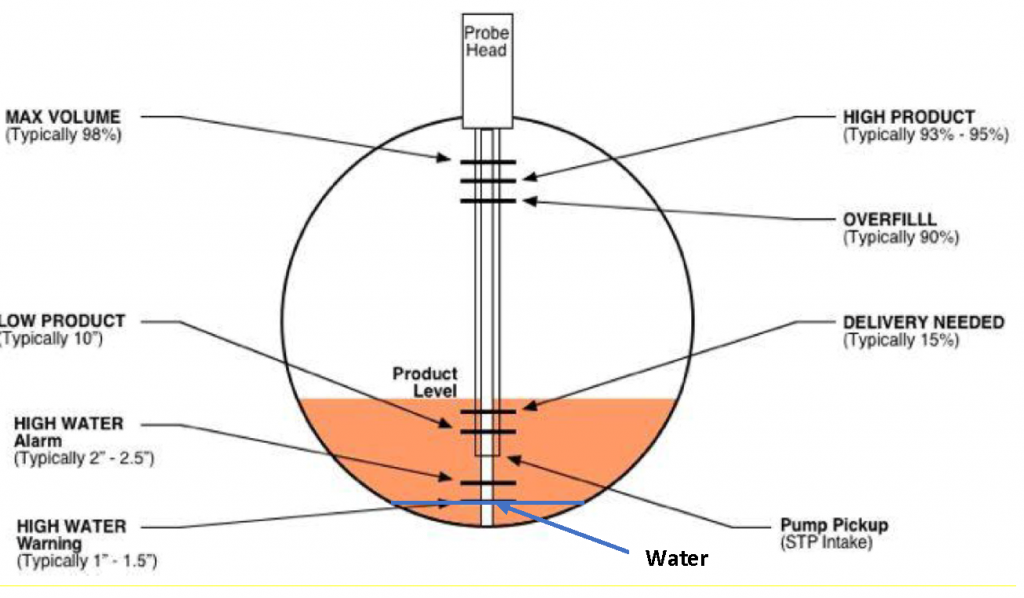
- Regularly monitor for water, especially after a major rain event. While automatic tank gauges and monitoring devices are good to use, realize their limitations. The image above illustrates a common issue. If you depend on a gauging system as your sole source of water identification, water will accumulate and cause an issue. Most systems do not register water until it is at least 1″ deep. In a typical 10,000 gallon tank, that is around 18 gallons of water. A single drop of water can support as much as 1 million microbes. One inch of undetected water is a serious problem. Regular fuel sampling can help alleviate the issue. Taking a quick bottom sample after a rain event and regularly once a month will help to rule out water contamination issues.
- Realize that water may not be easily accessed in your fuel system. All fuels systems are not the same. Even with diligent water management systems in place, water can still be a problem. Access is almost always limited and fuel samples are only as good as the location the sample is taken. Fuel tanks are constructed with strike plates underneath access points. Tanks are constructed with strike plates to insure the tank is not damage in the unforeseen case something heavy is dropped into the bottom or to reduce the possibility of wear from physically sticking a tank. Usually the strike plate is at least 12″ square and 1/4″ thick. If you sample over a strike plate, there could be 1/4″ of water in the tank bottom before it is ever indicated by sampling. Additionally, if the tank is tilted, water will migrate to the lowest point making it almost impossible to identify until it is too late. Know the tilt in your tank and understand how water can accumulate on the low end. Make an effort to find out if there is an accumulation taking place.
- Immediately remove water when found. This almost sounds too simple. However, take into account the limited access and use a company to remove the water that is knowledgeable as well. Have them take into account the tilt of the tank and the limits to proper access. Realize the cheapest solution may not be the best solution. If free water is left in the bottom of your tank, it will become a serious problem. You can expect higher maintenance costs and microbial influenced corrosion.
- Use a fuel biocide to kill microbial contamination associated with water in fuel. Water is always present! No matter how hard we try, there will always be some level of water. The best insurance is to use a quality fuel biocide that has high fuel solubility that works in both the fuel and water phases of a fuel system. Fact – water harbors microbes. Fact – biocides are the only way to kill microbes in your fuel and system.
The ideal fuel biocide should be designed to carry the the active ingredients throughout the fuel and fuel system. In order to achieve this goal, fuel solubility is critical. Equally critical is a biocide that efficiently partitions into any water phase present in the fuel. Biobor JF is the answer. It is a dual phase biocide that works to kill microbial growth in both the water and fuel. It is highly fuel soluble, developed to evenly distribute throughout the fuel and partition into water effectively killing microbes throughout the system. Microbial growth will occur in fuel systems with or without the presence of visible water. Eliminating free water is part of the solution. Good housekeeping is always a first line of defense against serious microbial contamination. However, the effective use of a biocide is the rest of the solution. Biobor®JF is effective at controlling microbiological growth in hydrocarbons both short and long-term. Laboratory experiments and the field studies verify this fact. Biobor®JF is a potent, fast kill biocide that provides long-term protection to fuel and fuel systems. The periodic treatment of your fuel system with Biobor JF is a proven method to controlling microbial contamination.
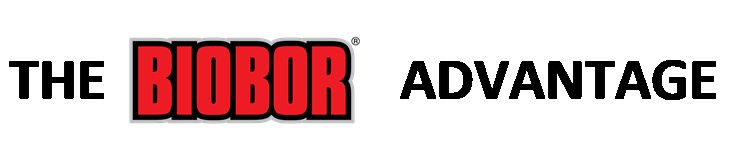
Share the Post